For years, Apple has relied on international supply chains to produce the iPhone. Most parts are made and assembled in countries like China, Japan, and South Korea, where labor is cheaper and supply networks are more efficient. But what if Apple moved all iPhone production to the United States? What if we had a fully Made in the USA iPhone?
It sounds like a patriotic move. But it might also be a very expensive one. In this article, we’ll explore how much a Made in the USA iPhone would cost, why the price would skyrocket, and whether it’s even practical for Apple to consider this shift.
Why the iPhone Isn’t Made in the USA
Before we calculate the cost, let’s understand why iPhones aren’t made in the U.S. in the first place.
1. Global Supply Chains
Apple works with hundreds of suppliers across more than 40 countries. These companies provide chips, cameras, screens, and other components. Then, everything is brought together in China, where the phones are assembled by companies like Foxconn.
This setup allows Apple to:
- Access cheaper labor
- Streamline production
- Manage inventory more efficiently
- Scale up quickly when demand spikes
2. Labor Costs
The average hourly wage for a factory worker in China is significantly lower than in the U.S. In China, wages can be as low as $3–$4 per hour, while in the U.S., manufacturing wages are closer to $20–$30 per hour—without including benefits.
Labor costs are a huge reason why American-made phones would be much more expensive.
The Real Cost of a Made in the USA iPhone
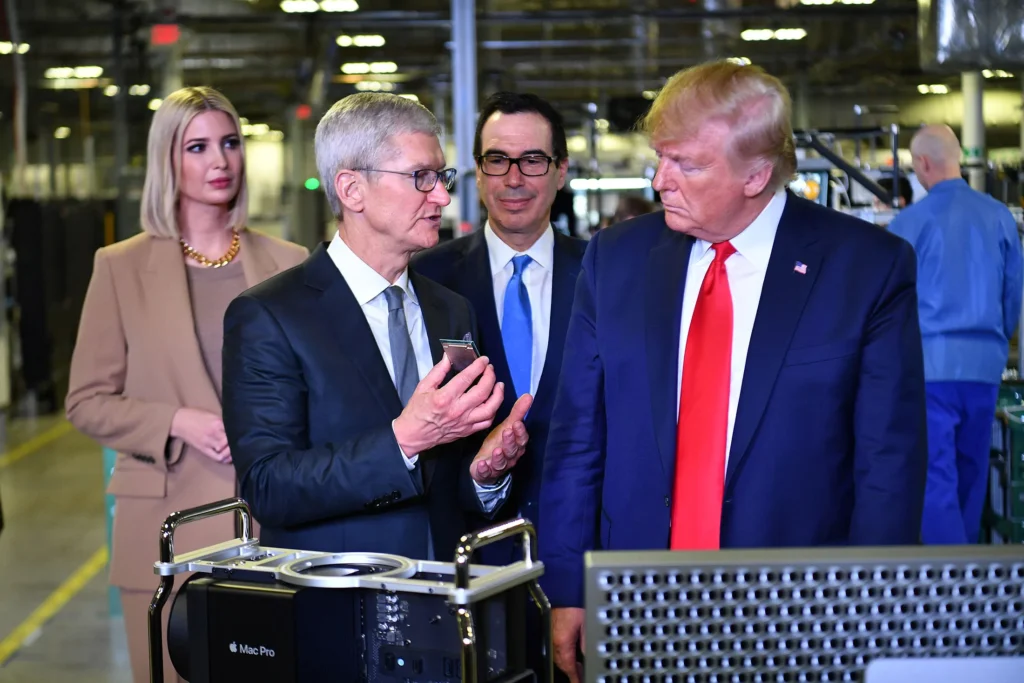
Now let’s get to the numbers. Multiple economic studies and industry estimates suggest that a Made in the USA iPhone could cost hundreds more than the current model.
Breakdown of Estimated Costs
Let’s take the iPhone 15 Pro as an example. Its base model currently sells for about $999. Here’s how the costs might change:
Cost Category | Current Estimate (Global) | Made in USA Estimate |
---|---|---|
Components | $500 | $500 (same) |
Assembly Labor | $10 | $70–$100 |
Logistics & Shipping | $20 | $10 (saves slightly) |
Corporate Overheads | $100 | $150–$200 |
Total Estimated Cost | ~$630 | ~$800–$900 |
Retail Price | $999 | $1,299–$1,499 |
That’s a jump of $300 to $500 for a phone with the same features—just because it’s assembled in the U.S.
Why the Price Difference?
1. Labor Is Expensive in the U.S.
As mentioned earlier, paying American workers means higher wages, benefits, insurance, and compliance with stricter labor laws. If Apple were to move final assembly to the U.S., labor costs could increase by nearly 1,000%.
2. Lack of Infrastructure
China has built massive industrial zones tailored for electronics. Foxconn’s factories employ hundreds of thousands of people and can produce millions of devices quickly. The U.S. doesn’t have that level of specialized infrastructure.
3. Skilled Workforce
While the U.S. has a skilled labor force, most aren’t trained in high-volume electronics assembly. Training workers would take time and money.
4. Higher Operational Costs
U.S. manufacturing also comes with more regulations—everything from environmental rules to workplace safety requirements. These add layers of cost and complexity to production.
What Parts Could Be Made in the USA?
Even though full iPhone production in the U.S. would be expensive, some parts of the phone already involve American companies.
- Apple’s Chips: The A17 Pro chip is designed by Apple in California and manufactured by TSMC in Taiwan. However, Apple is working with TSMC to open a chip factory in Arizona, which may lead to U.S.-made chips in the future.
- Glass: The iPhone’s glass is made by Corning, a U.S.-based company with factories in Kentucky.
These examples show it’s not impossible to manufacture components in the U.S.—but it’s not yet scalable for the entire phone.
Would Consumers Pay More?
This is the big question: Would people be willing to pay more for a Made in the USA iPhone?
Surveys suggest mixed results:
- Around 60% of Americans say they would prefer to buy U.S.-made products.
- But when the price is significantly higher, fewer people actually follow through.
If Apple charged $1,399 for a phone that looks and performs exactly like the $999 version, would enough people buy it? That’s doubtful.
Environmental Impact of U.S.-Made iPhones
Some might argue that local production would reduce emissions from international shipping. That’s true—but only to an extent. Setting up new factories, transporting parts within the U.S., and increasing power usage might cancel out those benefits.
Also, U.S. energy grids often rely more on fossil fuels than those in some Asian countries, where green energy is becoming more common in industrial zones.
Could Apple Move Production to the USA?
Technically, yes. Financially and logistically, it’s a massive challenge. Apple has already started to diversify its production away from China, moving some assembly to India and Vietnam. This strategy reduces risks tied to trade wars, tariffs, and political tensions.
But moving production to the U.S. would be on a whole other level. It’s not just about building a factory—it’s about building an entire ecosystem from scratch.
What If It Was Just Assembled in the USA?
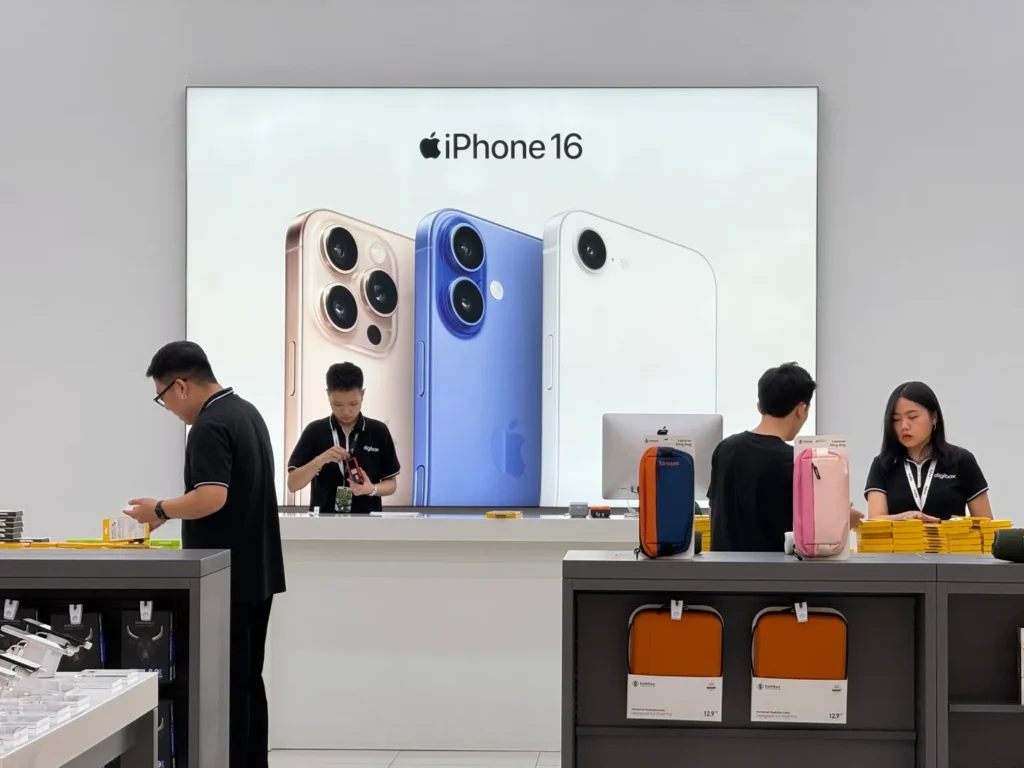
There’s a middle-ground approach: assemble iPhones in the U.S. using imported parts. This would still raise the cost but not as dramatically.
- Estimated cost increase: Around $30–$100 per phone
- Marketing value: Apple could advertise “Assembled in the USA,” which might appeal to patriotic buyers
- Impact on jobs: It could create thousands of U.S. manufacturing jobs
While this won’t make the iPhone 100% American, it’s a step that could be both affordable and meaningful.
Could Government Help Reduce Costs?
To support U.S. tech manufacturing, the government could:
- Offer tax breaks to companies like Apple
- Fund training programs for electronics workers
- Subsidize factory development
- Impose tariffs on foreign electronics (although this would raise prices for everyone)
Some of these ideas are already in motion. The CHIPS and Science Act, passed in 2022, aims to boost semiconductor manufacturing in the U.S. This could lead to more U.S.-made components in the future.
What It Means for the Future
The idea of a Made in the USA iPhone reflects a larger trend. Countries around the world are rethinking globalization and supply chains. The COVID-19 pandemic, chip shortages, and geopolitical tensions have shown the risks of overreliance on one region.
Apple may never make a 100% U.S.-built iPhone. But over the next 5–10 years, we’ll likely see more parts made in America—and maybe even more final assembly in the U.S.
It won’t be cheap. But it could be worth it.
Final Thoughts
The Made in the USA iPhone is an intriguing concept. It promises national pride, potential job creation, and a shift toward local production. But the price tag is real—and it’s steep.
A fully U.S.-made iPhone could cost $1,300 or more. And most buyers aren’t ready to pay that just for a “Made in America” label.
Still, partial steps like local assembly and chip manufacturing might strike the right balance between cost and domestic growth. As Apple continues to diversify its supply chain, we may see more American fingerprints on future iPhones—even if the whole device isn’t built here.
Read Next – Nvidia Made-in-USA Move Mirrors Trump’s Trade Strategy